
The average voltage and current fed to the load are controlled by switching ON and OFF between supply and load at a fast pace. The flux of the permanent magnet stator is constant in permanent magnet DC (PMDC) motor, field control method is not used in PMDC motors, and the speed of the motor changes solely with the back induced armature e.m.f. The pulse width can be adjusted by the controlled program or comparator circuits. Speed of the DC motor is directly controlled by applied voltage of the motor in Input voltage control method. The average value of the applied motor voltage is varied by applying a pulse width modulated (PWM) waveform to the motor. Speed can be varied with a wide range of smooth adjustment. Main feature of stepper motor is easy control like start, stop, forward and reverse directions.
#Position control of a dc motor arduino driver
Stepping motor driver excites rotor over a predefined discrete angular position. Viaene Jasper discussed characteristics of stepper motor and its step movement under open loop condition. The current in a winding needs to be reversed in order to reverse a magnetic pole. Bipolar stepper motors have a single winding per phase. A magnetic pole can be reversed without switching the direction of current.

Each section of winding is switched on for each direction of magnetic field.
#Position control of a dc motor arduino full
The motor shaft turns stepwise with an integer number of steps making a full rotation.Ī unipolar stepper motor has one winding with center tapped phase. Each pulse moves the shaft through a fixed angle. In open loop, stepper motor converts a train of input pulses into a precisely defined increment in the shaft position. Speed of stepper motor depends on the delay time between the steps. Step angle (i.e., constant angular position) depends on total number of steps per revolution. Stepper motor is controlled with two control parameters such as Step angle and Delay time between steps which are instructed by microcontroller. Performance of geared DC motor experimentally showed better result than commercial available stepper motors like 28BYJ-48 or STP-43d1027-01. GDCSM is suitable to hold and control vertical position of solar tracking system with low speed and step movement. If \(\varDelta\) value of GDCSM is less than or equal to − 0.4%, then it behaves like stepper motor. Performance of 10RPM & 30RPM GDCSM is analyzed with stepper motors in terms of Relative slip degree error per revolution ( RE \(_\mathrm\) or acceptable slippage degree tolerance value is less than or equal to 1%. Microcontroller ATmega 328P with switching delay time signals is used to control the geared DC motors. Speed of 10RPM & 30RPM geared DC motors is operated at 10V DC power supply. Stepping method resembles the step movement and controlling speed of the stepper motor. Combining effect of switching delay time signals A and D represents the Stepping Method. Controlling speed is implemented by using Step delay time signal (D) of microcontroller.
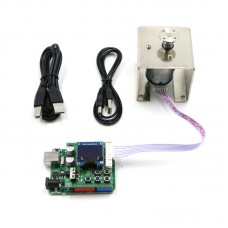
Speed of geared DC motor is controlled by passing fixed time interval between the pulses where the pulses have fixed width. Degree per step movement of geared DC motor is identified using Step angle switching delay time signal (A) of microcontroller. So, geared DC motor is implemented into stepper motor for low-speed applications using Stepping Method ( GDCSM). But it is cumbersome process to hold a solar panel at a particular vertical position depending on the sun’s position using low cost stepper motors. Degree of rotation is directly proportional to stepwise movement (stepping method) of stepper motor.
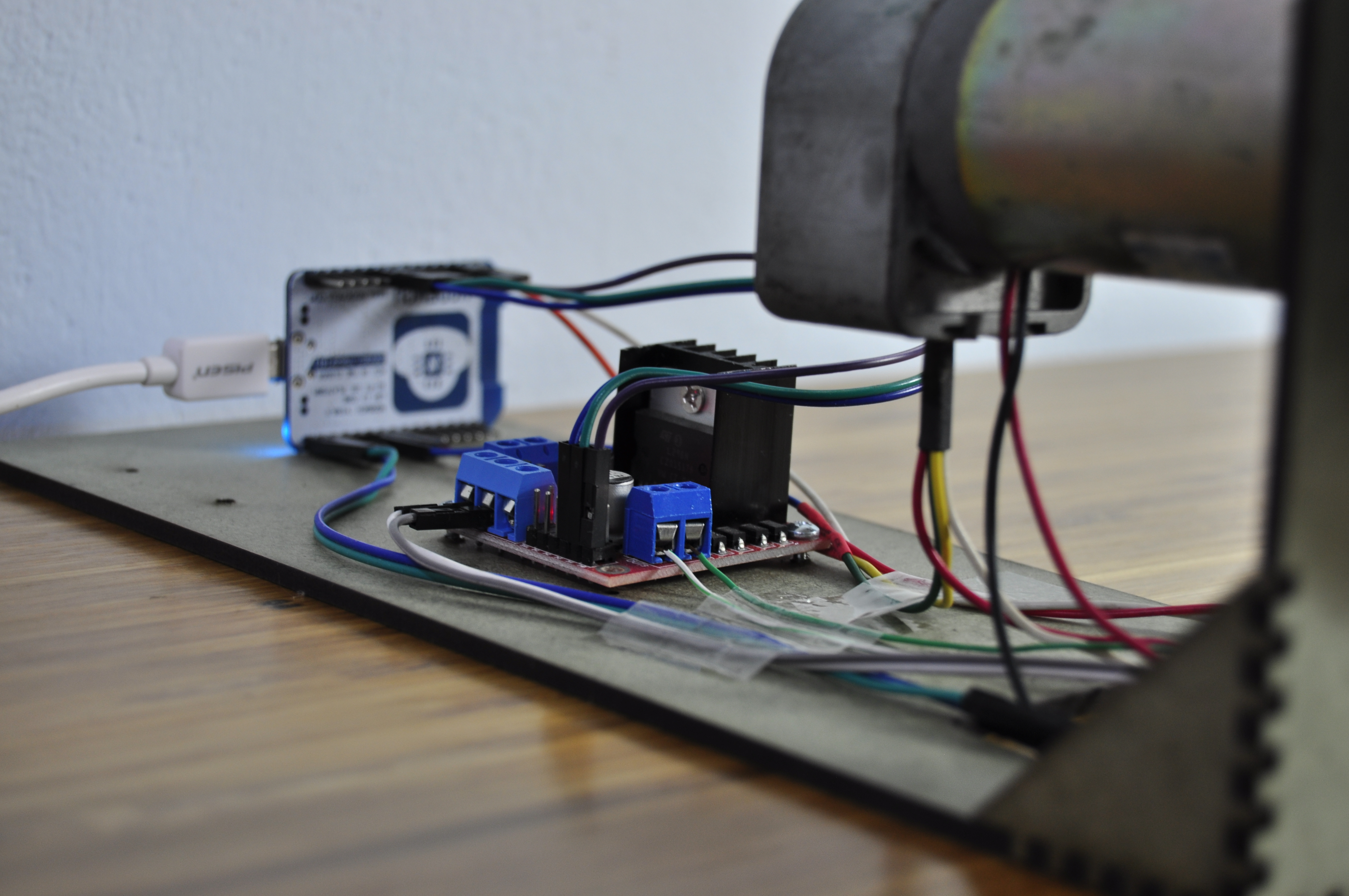
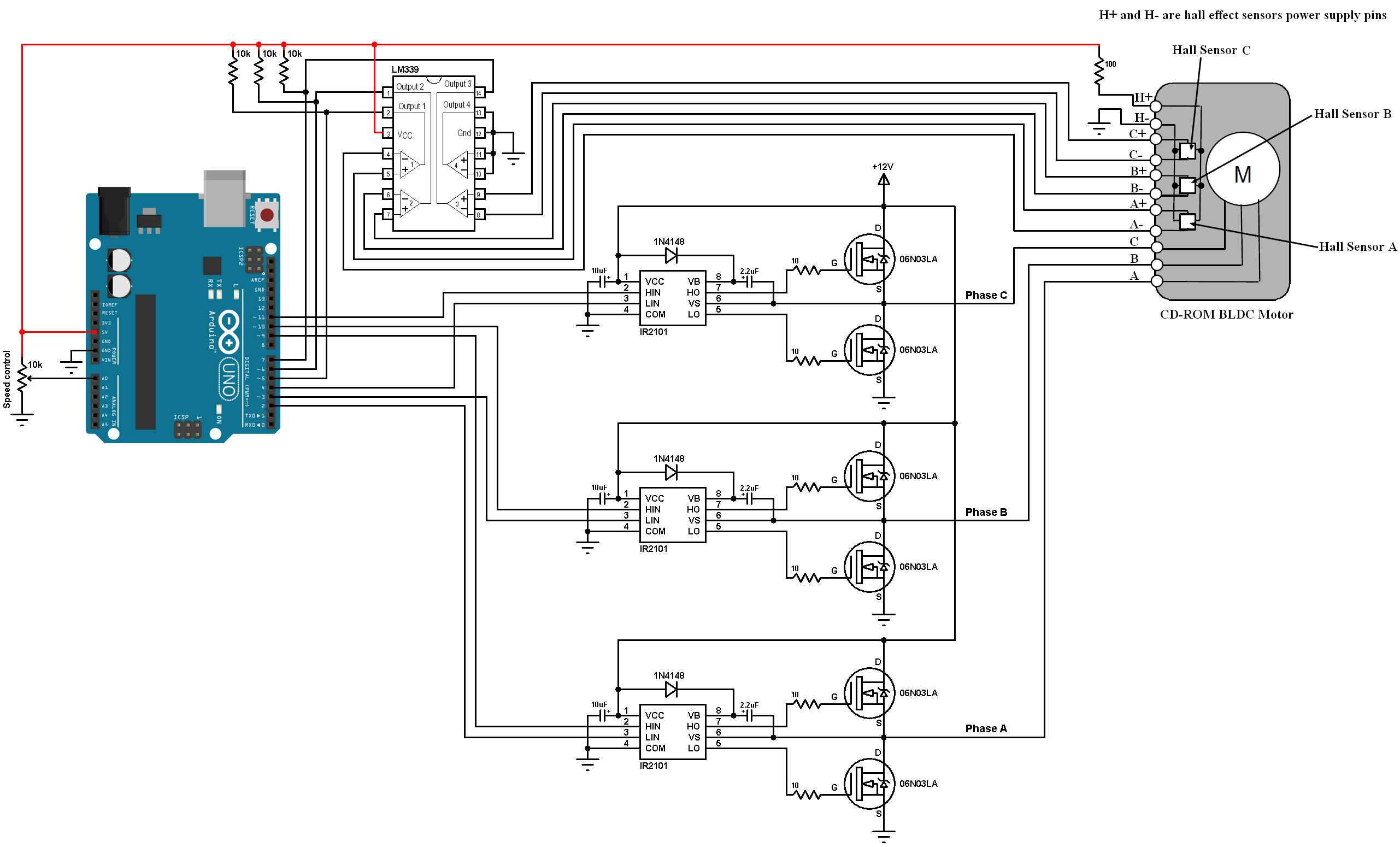
In solar tracking system, general stepper motor is used to control the stepwise movement and low speed of solar panel in vertical motion.
